大型精密構造体のコストダウン項目
材料選定によるコストダウン
鋳物は鋳型が必要なため、生産台数の多くない大型部品の場合はコスト高になります。また、鋼材のヤング率は鋳物より30%程度高いので、製缶は鋳物より軽量化も可能です。以上のような材料特性の差から、大型部品を設計する場合は、製缶製品の方が鋳物製品よりも、低コスト、短納期、高性能(高剛性、高い固有振動数)、軽量化を図ることが出来ます。
表面処理・防錆方法によるコストダウン
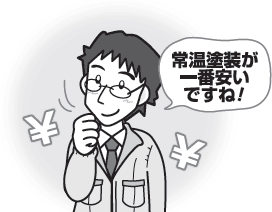
表面処理・防錆方法の選択によってもコストは大幅に変わります。一般的に、コストが高い順に並べると
- ステンレス材料の使用(表面処理なし)
- 無電解ニッケルめっきなどのめっき
- 焼付塗装
- 常温塗装
となり、常温塗装が最も安くなります。使用環境が屋内であれば、ほとんどの場合は常温塗装で充分です。充分な使用実績を有するアウトガスが発生しない常温塗装用塗料もあります。
構造最適化によるコストダウン
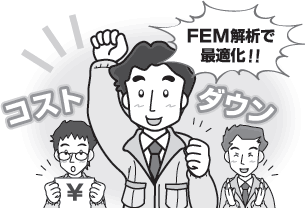
構造設計とFEM解析を適用して、性能上、必要な剛性と固有振動数を確保しつつ、軽量化を図り、更に組立・溶接が容易となるように、設計段階から構造最適化を図ることによって、大幅なコストダウンが可能になります。
ディテール設計によるコストダウン
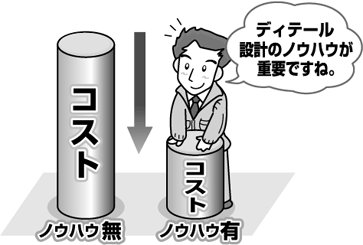
製缶製品は、板組の知識やディテールにコストダウンのノウハウがあり、ノウハウの有無によって大幅にコストの差が出ます。設計段階で部品コストの70%が決まると言っても良いでしょう。
いかに部品数を減らすか、組立しやすい形状、溶接しやすいディテールにするか、溶接量を必要最小限にできるか等がコストダウン設計の勝負です。
部品数を少なくすることによるコストダウン
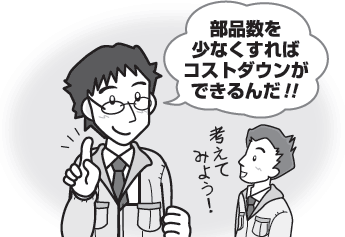
一つの部品に統合出来るものを2つに分けていませんか?例えば、剛性のある箱断面部品の上に、高精度のスライド面用プレート部品をボルトで締結したりしていませんか?
このような例では、製缶時から1つの部品に統合してしまえば、30%以上のコストダウンが可能です。更に、最終的な部品組立・ボルト締結のコストも無くなるのです。設計段階で徹底的に部品数を少なくすることで大幅なコストダウンが可能です。